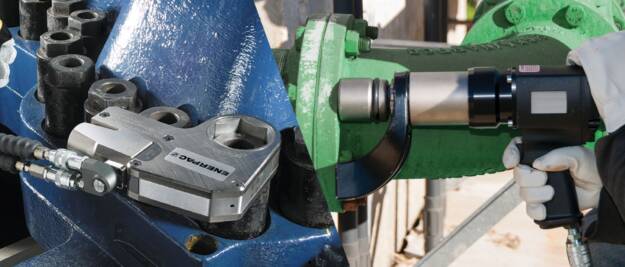
Hydraulic and pneumatic bolting tools utilize different types of media to generate power — hydraulics use liquids and pneumatics use pressurized air. While the fundamentals of the tools are similar, they each offer specific benefits that make them ideal for certain applications.
Read on for an explanation of the differences between hydraulics and pneumatics, as well as the pros and cons of each.
How Hydraulic Tools Work
Hydraulic tools use pressurized liquids to generate and transmit power. Typically, these tools run on ethylene glycol, mineral oil or synthetic liquid. Industrial hydraulic tools typically generate between 1,000 psi and 10,000 psi of power, though some specialized tools can generate over 20,000 psi. Compared to other types of tools, hydraulics are favored for their high torque capabilities, which are a massive benefit in industrial construction and large bolting assemblies with high torque requirements.
A hydraulic system is made up of several components:
- Hydraulic fluid
- A tank or reservoir to hold the hydraulic fluid
- Hydraulic pump
- Power source to operate the pump
- Hose to transfer the power
- Valves to control the flow direction
- Drive unit for cassettes
- Oil for lubrication
All these components are sold as individual pieces, but the full setup — pump, hose, tank, etc. — can pair with multiple tools. One downside of hydraulic tools is that they can be slower than other options.
Hydraulic hoses are rigid and unyielding, which can make navigating through a worksite challenging. Hydraulic tools themselves are usually less durable than other options; if workers are rough with the tools, pieces can fall off or break. To avoid leaks, you need to make sure that all fittings are properly assembled. If you are using multiple tools off of the same pump, you will also need to verify that you have the proper setup.
Safety
If the fittings are not correctly installed, hydraulic systems can leak, which can cause slip hazards. These tools can also produce an incredible amount of pressure, so it’s crucial that operators use utmost caution in keeping hands and limbs away from any pinch points when using the tool.
Applications & Uses
Hydraulic tools excel at tightening large bolts that other tools may not be able to handle, as well as projects that have high torque requirements. You’ll find hydraulic tools at work in aerospace, construction, heavy equipment and industrial sectors. Everyday applications of hydraulic systems include:
- Wind towers
- Large pipe flanges
- Oil field equipment maintenance
- Papermill equipment maintenance
- Water treatment plant maintenance
One place hydraulics are not favored is in food or medical systems, as the risk of contamination from hydraulic fluid is too high.
Hydraulic Tools: Pros & Cons | |
Pros | Cons |
|
|
How Pneumatic Tools Work
Pneumatic tools rely on pressurized air to operate. Tools range from small, handheld devices to large, full-facility systems. Typical pneumatic systems can generate around 80 psi to 100 psi of power.
Pneumatic tools require:
- Compressors
- Regulators
- Air tank
- Air lines
- Oil for lubrication
In cold temperatures, antifreeze is needed to keep the air lines from freezing. These tools may also require lubrication in the summer months. Air needs to be compressed before a pneumatic system is ready for use, which can cause short startup delays; however, once the system is ready to go, the tools can move very quickly.
Pneumatics can be more affordable to set up than hydraulics since they do not require as many accessories. However, the upkeep for pneumatic tools can be up to 10 times more expensive than hydraulics.
When used correctly and with proper precautions, pneumatic tools can be safe to operate. However, there are some factors operators should be aware of to keep themselves and others safe on the worksite.
Safety
Pneumatic tools are the heaviest option and often cause the most work-related injuries if not handled properly. The loud noises that the tools produce can lead to hearing loss or tinnitus (ringing in the ears), which is why earplugs or other ear protection is a must. Workers may also experience pain due to the vibration of the tools and the postures they need to maintain while working. The lubrication used in the air lines can create slip hazards, while the exhaust from the tools can potentially spread debris throughout the air.
Applications & Uses
Pneumatic tools are recommended when rundown speed is important, but tool accuracy is not. They are often used in biotech, pharmaceutical and food service applications. These tools are also used widely across the automotive, construction and manufacturing industries. Industrial applications of pneumatic tools include:
- Bridge construction
- Industrial construction
- Steel erection
- Fabrication shops
Some everyday applications of pneumatic systems include:
- Steel Structures – Air Impact Torque Wrenches
- Bridges – Air Impact Torque Wrenches
- Automotive Shops – Air Impact Torque Wrenches & Air Powered Shear Wrenches
- Residential and Commercial Projects – Air Impact Wrenches
Pneumatic Tools: Pros & Cons | |
Pros | Cons |
|
|
Hydraulic vs. Pneumatic Bolting Tools
Hydraulic Tools | Pneumatic Tools | |
Powered By | Pressurized liquid | Compressed air |
Required Components | Hydraulic fluid Occasionally, a tank to hold the hydraulic fluid Hydraulic pump Power source to operate the pump Hose to transfer the power Valves to control the flow direction Drive unit (sometimes with a cassette) Oil for lubrication |
Compressors Regulators Power source to operate the pump Air tank Air hoses Oil for lubrication |
Pressure Range | 1,000–5,000 psi 10,000+ psi for specialized tools |
80–100 psi |
Torque | 200 ft-lb. to 35,000 ft-lb. | 74 ft-lb. to 6,000 ft-lb. |
Cost | Less expensive to set up and maintain than pneumatic tools | More expensive to set up and maintain than pneumatic tools |
Contamination Risk | Moderate–high | Low–moderate |
Best For | Projects with large bolts or high torque requirements | Projects that require fast rundown |
How to Choose Between Hydraulic & Pneumatic Bolting Tools
Hydraulic and pneumatic systems are not used interchangeably because the technologies are geared toward certain applications. Hydraulic tools are best if your project involves tightening large bolts or requires a high amount of torque. For quick rundown speeds, pneumatic tools are often the go-to option.
The type of bolts you are using will also affect which option you choose. The bigger the bolt diameter, the more torque required to stretch the bolt. Hydraulic tools are most effective at handling large bolts with high torque requirements.
Electric Bolting Tools
There’s also another option. Electric bolting tools offer high accuracy, moderate speed and minimal noise levels, and are lighter than hydraulic and pneumatic tools. These bolting tools are the preferred option for projects with a large number of bolts. Instead of liquid or air to generate power, you will need access to a power source with sufficient voltage and heavy-duty extension cords (or, alternatively, the ability to charge batteries).