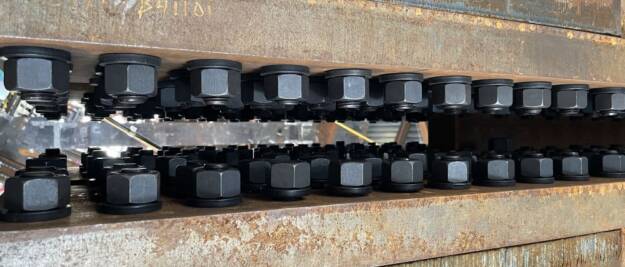
In structural bolting applications, “minimal clearance” refers to the limited space available around a fastener or component, which makes it difficult to access, manipulate or tighten bolts using standard tools. In these confined spaces, traditional bolting tools may be too bulky or obstructed by surrounding materials, leading to challenges in achieving proper torque application.
These cases require specialized tools — ones designed to fit into tight spaces without sacrificing performance or accuracy. Choosing the right tools for minimal clearance applications is essential to maintaining structural integrity, project timelines and, most importantly, worker safety.
Minimal Clearance Issues in Structural Bolting
When bolted connections are located in tight spaces, standard bolting tools often don’t fit or operate as intended. These restrictions directly affect workers on the job site, leading to inefficiencies and challenges that include:
- Difficulty achieving accurate torque: Restricted access can prevent proper tool positioning, leading to inaccurate torque application.
- Risk of damaging nearby components: Using oversized tools in tight spaces can lead to unintended contact and potential damage to surrounding materials.
- Increased labor time and costs: Difficult installations slow down productivity, increasing project timelines and labor costs.
- Ergonomic challenges for operators: Awkward tool positions may cause worker fatigue or strain, increasing the risk of injuries.
Where standard wrenches and torque tools fall short, specialized tight clearance tools can navigate obstructions and ensure safe, accurate fastener installation.
Minimal Clearance Tools and Technology
Innovations in tool design and technology have led to a range of high-performance tools that enable workers to access, tighten and verify bolts in confined spaces without compromising accuracy or efficiency.
The following tools were specifically developed to address the limitations of traditional tight-clearance solutions:
- Low-profile hydraulic torque wrenches: Compact and powerful, low-profile hydraulic torque wrenches fit into tight or recessed areas while delivering precise, high-torque output. They are designed with a thin, low-profile housing to navigate limited clearance spaces.
- Articulated or flexible-head torque wrenches: Adjustable, pivoting heads allow for better positioning and maneuverability in restricted spaces while maintaining accurate torque application.
- Crowsfoot or offset torque wrench adapters: These attachments extend a tool’s reach, providing access to bolts that are offset, recessed or obstructed. When properly calibrated, they enable accurate torque application at an angle, compensating for leverage discrepancies.
- Stubby wrenches: These short-handled wrenches are designed for tight spaces but do require more manual effort due to reduced leverage.
- Electric compact torque and shear wrenches: Both corded and cordless electric torque and shear wrenches provide power and mobility.
- Swivel socket extensions: Flexible attachments improve access and maneuverability around obstacles, enabling torque application at variable angles.
- Ultra-slim ratchets with multi-tooth gear systems: These compact, high-precision ratchets are designed for tight spaces, and feature fine-tooth gears for smooth operation while providing high torque output without compromising efficiency.
- Torque multipliers: Also known as “missing links,” torque multipliers increase torque output without requiring excessive force. They are invaluable for:
-
- Achieving high torque levels in minimal clearance applications.
- Reaching between a flange and bolt where other tools won’t fit.
- Ensuring precise torque application while reducing operator strain.
The Limitations of Tight Clearance Tools
While the tools listed above help address space constraints, they also come with limitations that can impact their performance or worker safety.
Tool | Primary Advantage | Challenge/Limitation |
Low-Profile Hydraulic Torque Wrench | High torque output in tight spaces | Requires a hydraulic pump; setup can be cumbersome compared to electric or battery-powered alternatives |
Articulated or Flexible-Head Torque Wrench | Adjustable head allows access to fasteners at difficult angles | If not positioned correctly, articulation can cause minor torque loss |
Crowsfoot or Offset Torque Wrench Adapter | Extends tool reach for recessed bolts | Requires torque correction calculations |
Stubby Wrench | Short handle design is ideal for confined work areas | Requires more manual effort |
Electric Compact Torque and Shear Wrench | Fast and precise torque application | Battery-powered models need recharging; Corded models require a power source nearby |
Swivel Socket Extension | Enables torque application at various angles when direct access is blocked | Added movement can slightly reduce applied torque, requiring compensation or recalibration |
Ultra-Slim Ratchet with Multi-Tooth Gear System | Fine-tooth gears enable smooth operation in tight spaces | Slimmer design could reduce durability in heavy-duty applications |
Torque Multiplier | Increases torque output with less effort | Needs a secure reaction point to function correctly, which may be challenging in minimal clearance areas |
Provided they have access to multiple tools, ironworkers may try sequential tightening in response to some of these challenges: switching between different tools to achieve better access and results. However, this obviously increases labor time and complicates the process — which is why it’s crucial to consult an expert in structural bolting to ensure you have the best tools for the job.
Best Practices for Addressing Minimal Clearance Challenges
By following these tips for tool selection, maintenance and integration, your team can mitigate clearance challenges while maintaining project timelines and structural integrity.
1. Thoroughly assess worksite conditions
Before selecting your tool, measure clearance dimensions, identify surrounding obstructions like beams or pipes and consider visibility limitations that could affect tool placement. A tool that fits in one spot may not be usable in another due to angle restrictions or interference from nearby components.
2. Match the tool to the application
Different bolting applications require different levels of torque and precision. For example, structural steel, aerospace and bridge construction require tools with integrated torque control to ensure accurate and repeatable results. Consider versatile tools that can handle multiple bolt sizes and torque levels to reduce the need for excessive equipment changes and improve overall efficiency.
3. Prioritize worker safety and ergonomics
Working in tight spaces often means dealing with awkward positioning, pinch points and physical strain. Select lightweight, compact tools with ergonomic designs to help minimize fatigue and the risk of injury. Ensure that tools do not create pinch hazards between the wrench, bolt or surrounding metal.
4. Maintain and calibrate tools regularly
Proper maintenance and calibration ensure tools remain accurate, efficient and safe for use in minimal clearance environments. Routine checks should include:
- Calibrating torque tools annually to maintain precision
- Inspecting tools before and after use for wear, damage or malfunctions
- Checking hydraulic hoses and corded tool brushes for leaks or power inefficiencies
- Cleaning and lubricating tools to prevent debris buildup and reduce wear
- Avoiding continuous operation at maximum torque, which can shorten tool lifespan
- Replacing worn-out parts and following manufacturer guidelines to maximize tool performance
5. Integrate new tools and technologies properly
Be sure to do the following when adopting new tools or solutions for minimal clearance applications to ensure smooth integration into existing workflows:
- Conduct a cost-benefit analysis to measure efficiency gains
- Implement tools in phases to minimize disruptions
- Provide comprehensive training to ensure workers use tools correctly
- Update safety protocols to account for new equipment
- Monitor tool performance and adjusting workflows as needed
Finding the Right Tools for the Job
We know that tight clearance bolting can slow down productivity, create safety risks and lead to costly rework. And because minimal clearance applications don’t have a one-size-fits-all solution, we do everything possible to find the right tool for your job.
At GWY, we specialize in high-performance bolting tools designed to tackle minimal clearance challenges with precision, speed and safety. Whether you need low-profile torque wrenches, compact shear wrenches, torque multipliers or customized solutions, we have the expertise and inventory to ensure your crew gets the job done faster and with less effort.